Time for change
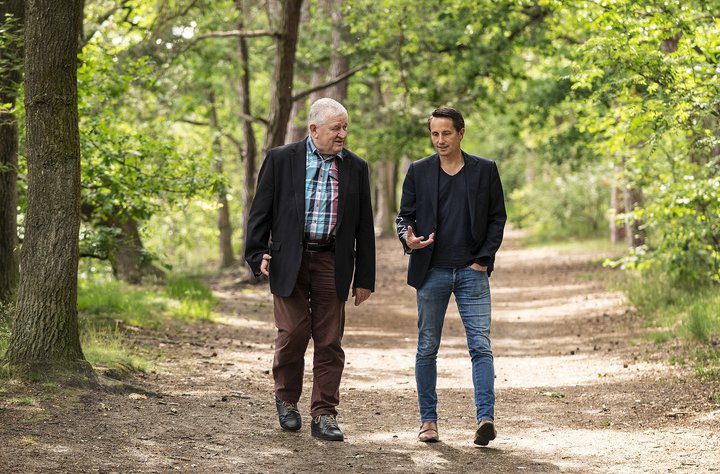
Solving the housing shortage calls for speed. Heijmans is picking up that gauntlet. Susanne van der Velden and Cyrille Pennavaire of Heijmans see a future in the industrialisation and digitalisation of residential building. “And we can do that more sustainably with timber-frame construction,” they say.
In the main building of the Brainport Industries Campus in Eindhoven, the domain of the high-tech manufacturing industry, anyone walking through the corridors will see robots and other technological breakthroughs. This is perfect spot for a conversation with Susanne van der Velden and Cyrille Pennavaire of Heijmans about the industrialisation and digitalisation of residential building at Heijmans.
Since 1 July 2022, Heijmans has owned an energy-neutral factory for the production of timber-frame building components in Heerenveen, in the province of Friesland. The acquisition of the former IIBO factory is a perfect fit with Heijmans' efforts to make its operations more sustainable and to accelerate the implementation of new, smart manufacturing technology. For knowledge and expertise on the latter, Heijmans is also partnering with the experienced timber-frame builder VDM, another Friesland-based company.
“We are really getting up to speed,” Susanne says. She is Heijmans’ brand-new Digitalisation programme director. “We are going to scale up production considerably in our new factory. Heijmans is planning to build an extra hall next to the existing factory in Heerenveen, which currently measures some two hundred by forty metres. This will make the factory more than twice as big. And it will be up and running in the summer of 2023.”
For Cyrille Pennavaire, Building Information Model (BIM) manager at Heijmans, the advantages of industrialising timber-frame construction are obvious. “It will enable us to increase our housing production, complementing the homes made of other materials we already build. This will enable Heijmans to meet its social responsibility in the public housing task the country is facing. Because the housing shortage in the Netherlands is enormous. The Ministry of Housing and Spatial Planning has asked the construction industry to build 100,000 homes a year. And quite rightly, because no one wants to live at home with mum and dad forever.”
Thanks to the industrialisation of timber-frame construction, Heijmans can also make a substantial contribution to the required sustainability of the built environment. The lower weight of a timber-frame house saves materials, emissions and transport costs. Timber production is more sustainable anyway: after all, timber is a renewable material and stores CO2.
But is industrialising timber frame construction a simple matter? No, it’s about as challenging as a four-star sudoku, mainly because production has a range of speeds. For example, each robot – used to apply stone strips, sometimes in different colours - has its own speed. Different components also require different drying times.
Another logistical puzzle is matching production to transport. If you want to deliver four houses every day, you need twelve trucks. That requires well thought out loading and unloading. Susanne smiles: “The trick is to streamline all the processes.”
Effective inventories management is particularly crucial, Cyrille argues. “At the factory, you don’t want to have too much under your roof, because they are large components. But nor do you want assembly teams to be out of work. They are leading.”
These plans are all based on digitalisation. Digital building benefits both Heijmans and its clients. The advantage for the builder? Cyrille: “In the past, you went out and produced drawings for every project. The digitalisation of the process gives us much more knowledge and real-time insight in advance, so we can organise the construction project more efficiently and effectively.”
Susanne sums it up in one sentence: the industrialisation of standardised timber-frame construction is basically a shift from engineering to configuration. For instance, from 2023 clients will be able to use Heijmans’ 3D Home Configurator to put together their own timber-frame house. At home on their computer or tablet, and at their leisure. “Do you want number 23 on the plot map? Okay, just click on it,” Cyrille laughs. “Then you can choose and add on: the kitchen in front or at the back, bay window or not, room in the attic or a dormer window, et cetera.”
There is certainly a range of options. But Heijmans also wants to avoid causing stress from too much choice. Susanne: “A huge bin of Lego bricks that you pour out in front of someone won't make anyone happy.” She expects the 3D Home Configurator to start by offering various basic styles - from budget and space to (extra) sustainability. What is technically possible next? The world of zeros and ones leaves no room for doubt: if a client can digitally configure their home, they know that Heijmans can also build it.
The trick is to streamline all the processes
Timber frame construction and digitalisation are a perfect fit with Heijmans’ mission to create healthy living environments. Digitalisation also gives Heijmans more rapid insight into the footprint of the materials used and gives the company the opportunity to adapt products more quickly to future housing wishes and sustainability requirements. “Because it’s about more than just living,” Cyrille stresses. “The 3D Home Configurator also makes you think about what you want in terms of your garden, your shed or your yard fence. And on the sustainability front: traditionally, we used to deposit yellow sand in gardens. Now we deposit black soil, to plant trees in.” Susanne agrees: “You can also opt for a sedum roof, nesting boxes, butterfly stones or a bee border.”
Do they believe timber is the future? Right down to their annual rings, they say. Cyrille recalls a memory: “I lived in New Zealand for three years. There, it’s customary for your parents to plant trees at your birth, so you can cut them down later and use them to build a house. That’s a nice tradition.” And the fascination with industrialisation and digitalisation? Susanne, laughing: “I’m a child of the Eindhoven region.” Additional assets: her studies in Economics and Management at Tilburg University, where she is currently writing a dissertation on the history of ASML from the perspective of innovation management. Cyrille spontaneously adds: "I’m really happy with her arrival. It’s great that Heijmans is bringing in this expertise.”
We bid farewell to the Brainport Industries Campus. This huge complex is surrounded by hundreds of trees, with the Norway spruce or Picea abies the most common species. This Scandinavian tree provides spruce wood, the material of choice for timber-frame construction. But not today. This day was for planting a tree. A promising one, with sturdy roots.